We supply welded stainless steel tubes in a wide range of dimensions and designs, the alloys include austenitic, ferritic stainless steel, also duplex, and specific high alloys grade, welded tubes can be straight or U-bent and smooth or with enhanced surface, furthermore, tubing shape can be round, oval, square or rectangular with length ranging from up to 30 meters. Welded Tubes are commonly used in the automotive, food and beverage, energy, construction, oil and gas and chemical industries.
Welded tube is manufactured from stainless steel strips or sheets into a tube shape and then welded the seam longitudinally. The weld seam can be left beaded or it can be further worked by cold rolling and forging methods. The welded tube can also be drawn similarly to seamless tubing to produce a finer weld seam with better surface finishes and tighter tolerances.
ASTM standard specifications for welded tube & pipe have ASTM A 269, ASTM A 249, ASTM A268, A312, A554, A789, or other standards. We supply a variety of grades of stainless steel including 304/304L and 316/316L in standard and custom sizes and dimensions.
Our Advantages
- Quality Manage system
- Wide range of sizes
- Variety of grades including Special alloys
- Custom properties and finishes
- Tighter tolerances
- In-home tests
- Unique packaging
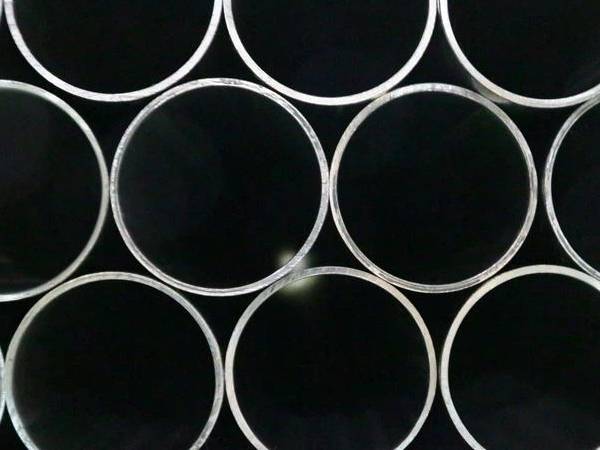
Welded Tube and Pipe Specifications
SPECIFICATION | ALLOYS INCLUDED |
---|---|
ASTM A249/SA249 | 304, 304H, 304L, 304N, 304LN, 316, 316L, 316N, 316LN, 317L |
A268/SA268 | 405, 409, 439, 446 |
ASTM A269 | 304, 304L, 304LN, 316, 316L, 316LN, 317 |
A789/SA789 | 2003, 2101, 2205, 2507 |
A688/SA688 | 304, 304L, 304N, 304LN, 316, 316L, 316N, 316LN |
A803/SA803 | 409, 439 |
A-1016/SA-1016 | General requirements for ferritic alloy steel, austenitic alloy steel and stainless steel tubes |
B704/SB704 | Welded UNS N06625 and UNS N08825 alloy tubes |
ASTM A312/SA312 | 304, 304L, 316, 316L, 316H, 321/321H, 347/347H |
DIN EN 10357 | 1.4301, 1.4306, 1.4845, 1.4401, 1.4404, 1.4571, 1.4541, 1.4550 , 1.4539, 1.4462 |
EN10217-7 | 1.4301, 1.4306, 1.4845, 1.4401, 1.4404, 1.4571, 1.4541, 1.4550, 1.4539, 1.4462 |
EN 10296-2 | X5CrNi18-10 , X2CrNi19-11 , X12CrNi25-21 , X5CrNi17-12-2 , X5CrNi17-12-3 , X2CrNiMo18-14-3 , X6CrNiTi18-10 , X6CrNiTb18-10 |
304/304L, 316/316 Stainless Steel Grades
304 Stainless Steel Welded Tube
As the most widely used of all stainless steel grade, 304 stainless steel tubing offers good corrosion resistance to many chemical corrodents, as well as industrial atmospheres. 304 stainless steel tubing offers good formability and can be readily welded by all common methods. An extra low-carbon variation, called 304L, avoids harmful carbide precipitation due to welding. This variation offers the same corrosion resistance as 304 but with slightly lower mechanical properties.
304 Welded Stainless Tube offers a great mix of strength and corrosion resistance in most situations outside of marine environments.
304 Stainless Steel Chemical Composition
Grade | C | Si | Mn | Cr | Ni | S | P | Fe |
---|---|---|---|---|---|---|---|---|
304 | 0,08 | 1,0 | 2 | 18 – 20 | 8 – 11 | 0,03 | 0,045 | Bal. |
316 Stainless Steel Welded Tube
316 stainless steel tubing is more resistant to corrosion and pitting than 304 stainless steel and offers higher strength at elevated temperatures due in part to the addition of molybdenum. 316 stainless tubing is ideal for such applications as pumps, valves, textile and chemical equipment, pulp & paper, and marine applications. In addition, 316L is an extra low-carbon variation that helps avoid carbide precipitation due to welding.
The increased performance of 316/316L stainless steel makes it better suited for environments rich in salt air and chloride.
316/316L Stainless Steel Chemical Composition, %, Max
Grade | C | Mn | P | S | Si | Ni | Cr | Mo | Fe |
---|---|---|---|---|---|---|---|---|---|
316 | 0.08 | 2.00 | 0.045 | 0.030 | 1.0 | 11-14 | 16-18 | 2-3 | Balance |
316L | 0.035 | 2.00 | 0.045 | 0.030 | 1.0 | 10-14 | 16-18 | 2-3 | Balance |
Applications
Boiler, Heat Exchanger and Condenser Tube
We supply heat-treated stainless steel tubes in coil or straight formats with lengths up to 30 meters. Our complete range of tubes is also available in different types of alloys including austenitic, AISI 300 series, and nickel-content alloys. We remain one of the leading manufacturers of tubes for heat exchangers and heating elements with high-quality standards.
Mechanical Tubing
Stainless steel tube products are manufactured from austenitic steel alloys that provide excellent strength and advanced corrosion resistance. Austenitic stainless tubing products, including stainless 316 tubing and 304 tubing are available in round, square, and rectangular shapes to support various applications.
We provide you with numerous size and shape options for stainless steel tube needs. Whether it is round, square, or rectangular tubing, we can provide you with welded stainless steel tubing that meets exact specifications.
We offer both a wide array of diameters and thicknesses and the ability to customize your order via our stainless tube processing services. We even produce laser-cut tube parts. Our welded tube includes the following stainless tubing selections:
Shape | Grade/Type | Stainless Steel Tube Sizes |
Stainless Steel Rectangle Tube | Grades: 304/304L, 316/316L Type: Polish, Mill Finish, Welded-Ornamental | Widths 0.5″ thru 8″ Wall Thickness: up to 0.25″ |
Stainless Steel Round Tube | Grades: 304/304L, 316/316L Type: Polish, Mill Finish, Welded-Ornamental | OD: 0.1875″ thru 6″ Wall Thickness: up to 0.25″ |
Stainless Steel Square Tube | Grades: 304/304L, 316/316L Type: 180 Polish, Mill Finish, Welded-Ornamental | Widths 0.5″ thru 6″ Wall Thickness: up to 0.25″ |
Welded Stainless Steel Round Tubing
Stainless steel 304s provides increased strength and workability and is ideal for structural applications where extreme pressure is not involved or for internal applications where aesthetic appearance is not important. Stainless steel round tube 304 provides excellent strength and durability, is easy to cut, bend, and form, and is versatile and affordable enough for a broad spectrum of applications.
Stainless steel 316 round tubing is welded in structure and possesses great durability under pressure, with a higher aesthetic appeal than stainless 304 tubing. Also referred to as surgical stainless steel, 316 round stainless steel tubing is commonly used in the food and pharmacy industry where it is required to minimize metallic contamination.
Welded Stainless Steel Square Tube
Stainless steel square tubing contains a minimum of 10.5% chromium content by mass, which imparts natural anti-corrosion properties that allow it to be used with harsh or acidic chemicals, fresh water, and salt water. Stainless steel square tube also provides excellent strength, durability, and corrosion resistance.
Welded Stainless Steel Rectangular Tube
Stainless steel rectangular tube provides an outstanding combination of strength, durability, and corrosion resistance. SS rectangular tubing allows it to withstand chemicals, fresh water, salt water, and more, making it ideal for outdoor installations and other harsh environments where carbon rectangular steel tubing would quickly fail.
Re-Drawn & Precision Stainless Steel Welded Tubes
Stainless steel welded tubes can be non-standard size, thin-walled, or have a tight tolerance, these high-quality steel tubes are available in coil form, straight lengths, or short pieces in a large range of sizes.
Stainless Steel grades and Nickel and Corrosion Resistant Alloys are for use in critical applications in the following industries: Aerospace, Automotive, Chemical Processing, Industrial Heating, Medical Devices, Nuclear Power Generation, Renewable Energy, Oil, and Gas Upstream, and Oil and Gas Downstream.
Welded Stainless Steel Tube Sizes
These again can be supplied in coil or alternatively fixed straight lengths and if required cut into smaller pieces. Tube sizes available in coils range from 3.0 mm – 38.0 mm, and in straight lengths from 3.0mm – 304.0mm in a wide range of Stainless Steels and Nickel Alloys. We offer an extensive range of Welded Tubes supplied in Standard Metric or Imperial sizes. Unique size is available for your project on request.
Producing Process
Stainless Steel Welded Tube Manufacturing
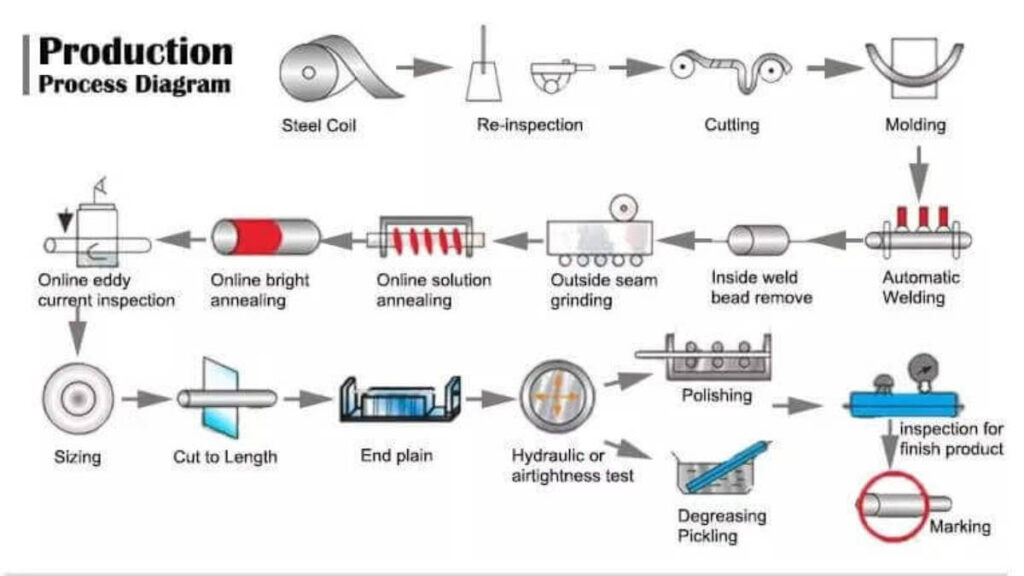
Tube Manufactured from Coil
We use fully-automated TIG welding production processes from coil to weld tube, it is the most technically sophisticated and economical process for manufacturing longitudinally welded tubes. , we have more than 150 roller sets to produce tubes customized to custom sizes, special materials, or particular tolerance requirements in continuous production, also standard sizes.
On production lines, we produce tubes from coil with outside diameters ranging from 3.0 to 762 mm, with wall thicknesses up to 12.7 mm. The standard lengths are 6 m. Fixed lengths or lengths up to a maximum of 20 m can be produced in a number of sizes without circumferential welding, for coil tubing, the length can be up to 2500 meters.
Pipe Manufactured from Plate
We produce longitudinally welded pipes with wall thicknesses of up to 70 mm and an outside diameter of up to 2 032 mm (80″) from individual steel plates – in standard dimensions as well as custom sizes. We produce manufactured lengths of up to 12 m without circumferential weld, and up to 24 m with circumferential weld.
Certificates & Quality
Quality and Tests
Dingshang Stainless is proudly certified according to ISO 9001 , ISO 14001 and PED.
Since its founding, our factory has striven to meet the highest standards demanded by customers and national and international standards. our Quality Department is formed by professional experts who are in charge of guaranteeing the QUALITY of the products delivered. We offer a wide range of destructive and non-destructive testing methods.
Non-destructive Tests: | Destructive Tests: |
Radiographic examination / X-ray testing Ultrasonic testing Eddy-current testing Visual inspection Leakage testing Dye penetrant testing and magnetic particle testing Water pressure testing Surface roughness measurements | Tensile test Impact test Technological testing (e. g. bending test) Hardness test Metallographic examination Corrosion test Spectroscopy |
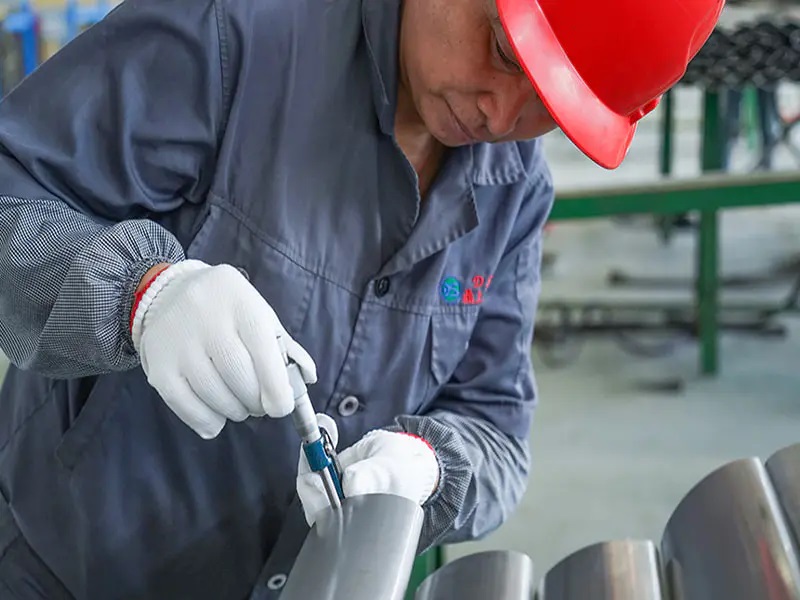
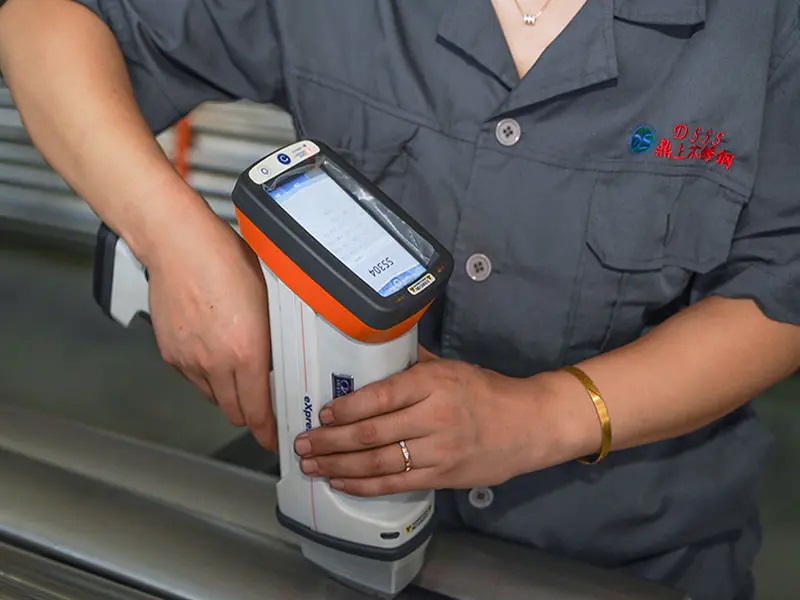
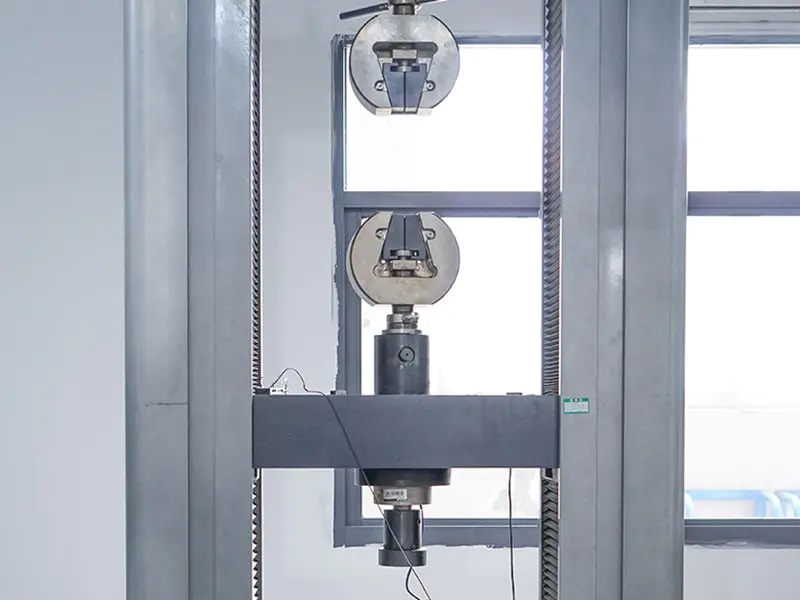
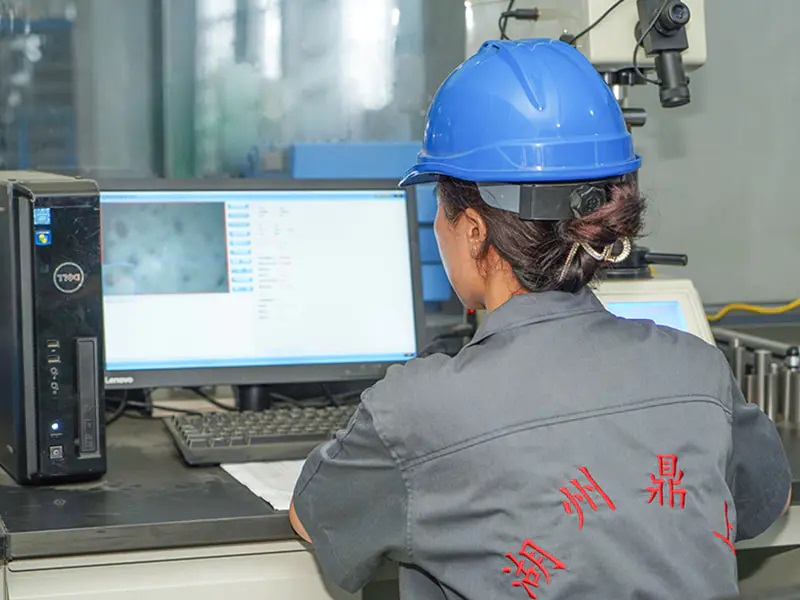
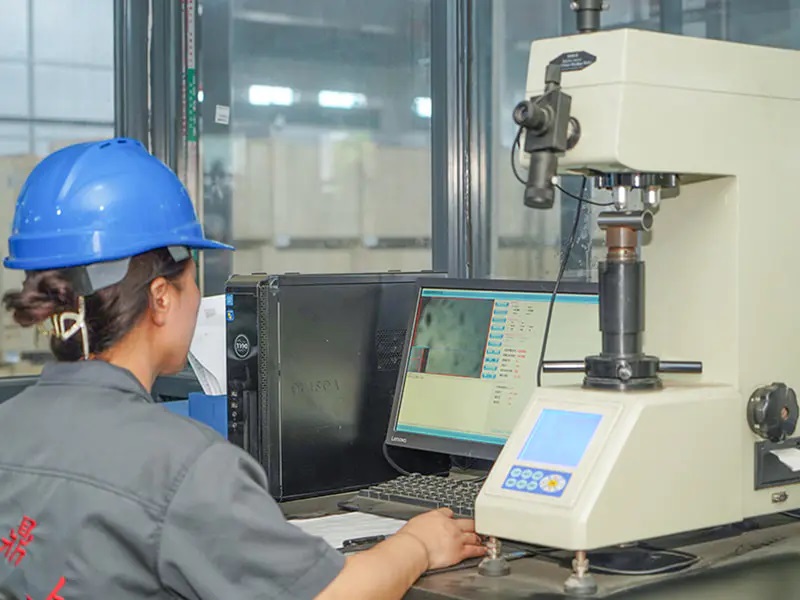
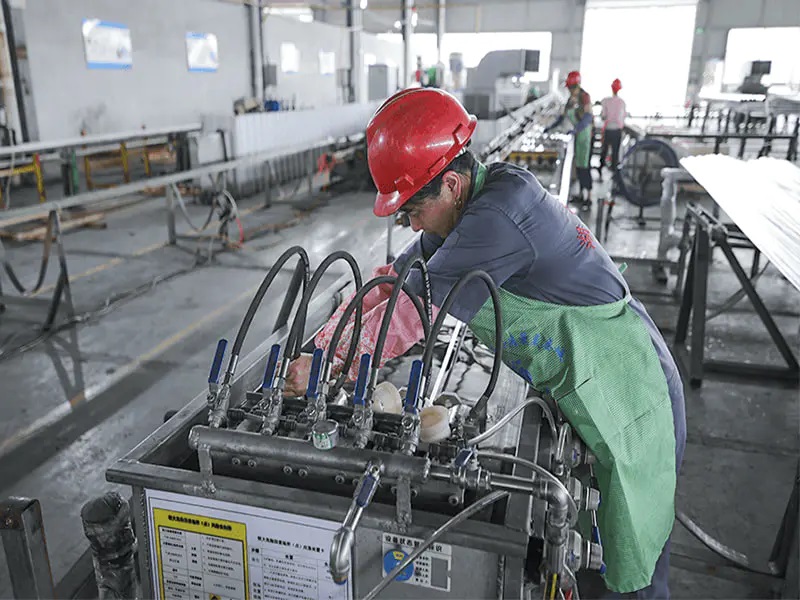
Our technicians work hard to evaluate and homologate manufacturers and mills, monitoring manufacturing and material testing. We verify testing and MTCs, controlling each material supplied to our customers.
We are able to produce welded tubes to precise specifications, meeting the strictest requirements of clients regarding the quality of materials, composition, and mechanical qualities.
Typical Tube Welding Processes
- Electric Resistance Welding (ERW)
- High Frequency Welding
- Laser Beam Welding
- Gas Tungsten Arc Welding (TIG welding)
- Plasma Arc Welding
- Submerged Arc Welding
Electric Resistance Welding (ERW)
Low-frequency welding, accomplished through a rotating copper electrode, is used most often for mild steel tube from .250 to .375 inch in diameter. This process is most suitable for the smallest diameters, as the impeders needed for HF welding cannot fit into the tiny tubes. As the welding transformer rotates, the copper electrodes come into contact with the tube edges, heating them so that they can be welded.
Gas Tungsten Arc Welding (GTAW)
GTAW is used for pressure-quality welds on 300 series stainless steel at slower welding speeds. It produces a good weld with little bead.
A welding torch with a tungsten tip, usually employing argon or an argon/oxygen mixture, heats the edges of the strip until the metal begins to melt or puddle, and the next pair of rolls squeezes the strip edges together. Here, edge registration is critical.
Laser Welding
The cost of laser welding is high relative to that of GTAW, although it is faster. It is used primarily for exotic metals and 300 series stainless steel, though some manufacturers use it on 400 series stainless.Laser welding produces the smallest heat-affected zone (HAZ) and a bead even smaller than that produced by GTAW. Since there is almost no change in the grain structure of the parent metal, the finished piece has greater flexibility than a GTAW part. However, with this technique, edge registration is more critical than with the others.